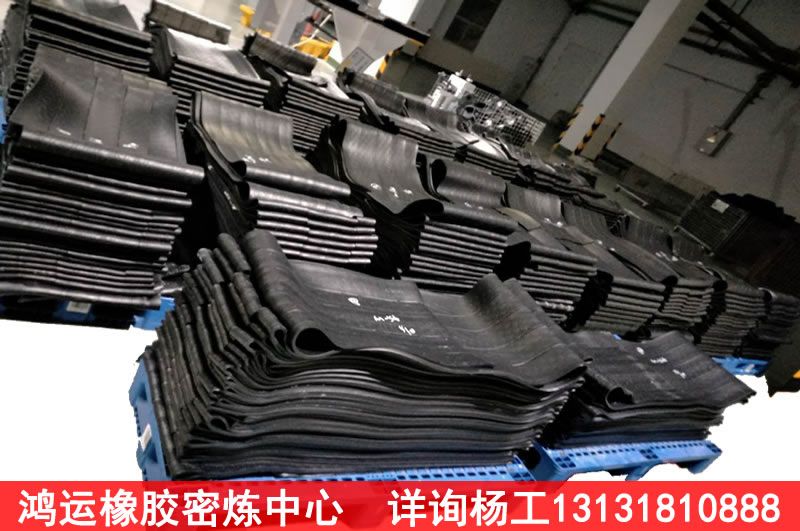
Generally, units and factories use sealed rubber mixers for the mixing of tire recycled rubber. Its biggest characteristics are high efficiency, uniformity, high degree of automation, strong controllability, simple operation, and low dust pollution. The operation of rubber mixer is relatively simple, which can reduce employee training costs and operational difficulties. Rubber mixer is a device used for mixing, shaping, and processing rubber raw materials. It can mix rubber raw materials with various fillers, plasticizers, stabilizers, vulcanizers, etc. to prepare rubber products with various properties. When using a rubber mixer, the operator needs to put the rubber raw materials into the feeding port of the mixer, then start the equipment for mixing and molding, and finally obtain the required rubber mixture. Many factories are still using open type rubber mixers for mixing tread recycled rubber, because open type rubber mixers have high flexibility and are particularly suitable for mixing rubber varieties, hard rubber, sponge rubber, etc
The dosing sequence of tire regeneration rubber mixed with a mixer is particularly important, as different feeding sequences may lead to white spraying, blue spraying, roller sticking, and different hardness. The recycled tire rubber is into the gap the rollers along one end of the roller, and the roller distance is controlled 2-2.5 mm for about 5 minutes of rubber mixing. The recycled rubber on the tread is wrapped in a smooth and seamless mixing film on the front roller. When there is still 20% of the accumulated rubber on the roller, antioxidant and accelerator are added, and the rubber is mixed multiple times to evenly disperse the antioxidant and accelerator in the rubber. Adding anti-aging agents first prevents thermal aging or scorching during high-temperature rubber mixing. Some accelerators have a plasticizing effect on the rubber material. Next, zinc oxide can be added, and then a very small amount can be added when adding carbon black, because some rubber rolls off as soon as carbon black is added. If there is any sign of roller detachment, stop adding carbon black and wait for the rubber material to be smoothly wrapped on the roller before adding carbon black. There are roughly three methods for adding carbon black
1. Move the carbon black back and forth along the roller from left to right to add
2. Add carbon black from the middle of the roller and flip the two sections of rubber to the middle
3. Add carbon black from one end of the baffle and flip the adhesive from the other side of the baffle
Adding carbon black from the middle of the roller or one side of the baffle is not easy to cause roller detachment, and even if there is a phenomenon of roller detachment, it is only a small part and not easy to completely detach the roller. After adding tread recycled rubber material, loose carbon black is easily compressed into flakes after being removed from the roll. After re rolling, carbon black is not easily dispersed, especially when mixing hard rubber, sulfur yellow is difficult to disperse when pressed into flakes. Whether it is re refining or thin pass, the yellow pits on the film cannot be changed. So when adding carbon black, it should be added less and more frequently, and do not pour all the carbon black onto the roller at once
The early stage of adding carbon black is the fastest time for "eating". At this point, do not add softeners. First, add half of the carbon black and then add half of the softener, which will accelerate the "eating" process. Add the other half of the softener along with the remaining carbon black. During the process of adding powder, the roller spacing should be gradually relaxed to keep the accumulated rubber within 20-30%, allowing the powder auxiliary materials to naturally enter the rubber and fully mix with the recycled rubber on the tread evenly. Do not perform cutting operation at this time to avoid affecting the quality of the mixed rubber. If the weight of the auxiliary material softening plasticizer is relatively large, the carbon black and softener can be made into a paste and added
Stearic acid needs to be added later, and teaching too early can easily cause the mixed rubber to roll off. It can be added when there is still some carbon black in the roller, and the vulcanizing agent must be added in the later stage of rubber mixing. After all the ingredients are added, further refining is necessary to ensure even mixing of the rubber material. The usual methods of refining include "Eight Knives", "Triangle Wrap", "Rolling", "Thin Pass", and other methods 23Y5y18.
1. The origin of "Eight Knives" is to cut the rubber at a 45 ° angle along the roller direction four times, and then pile up the rubber material on the roller. The purpose is to evenly mix the vertical and horizontal rolling, and the cutting operation is eight times, so it is commonly known as "Eight Knives"
2. The "triangular bag" is used to wrap the mixed rubber into a triangular bag on the roller, making the feeding of the mixed rubber more uniform
4. Rolling "refers to cutting the mixed rubber on the roller with one hand, and rolling the mixed rubber into a cylindrical shape and mixing it on the roller with the other hand, so that the recycled rubber on the tread I is evenly mixed longitudinally
The "triangular bag" and "rolling" methods are not conducive to the heat dissipation of tire recycled rubber, and are prone to scorching. The labor intensity of mixing rubber after 5-6 minutes of flipping is high, which affects production efficiency. The "Eight Knives" have a good mixing effect on the vertical and horizontal forces of the adhesive, moderate labor intensity, and even mixing of the adhesive. All "Eight Knives" are ideal operating methods
After the tire recycled rubber mixture is turned over, it is thinly penetrated. Bo Tong can effectively disperse the mixture. The specific operation method is as follows:
1. Adjust the distance the rollers to 0.5-1mm, and add the mixed rubber material so that all its weight naturally falls into the material tray
2. Repeat the above steps 5-6 times, then rotate the mixed rubber by 90 ° and repeat the above steps again. Cooling of the rubber roller is particularly important during the thin pass process, and caution should be taken to prevent scorching during the thin pass process
3. After all the reclaimed rubber on the tread is thinned, adjust the roll pitch to 4-5mm. Put a small piece of rubber on the roller to punch out the roll pitch. Directly putting all the rubber into the roller will easily cause equipment damage
4. After rolling through the front roll of the entire package, it will be refined for 2-3 minutes and cooled down
Thin pass can more evenly disperse the additives in the formula. Through repeated high-speed shear thinning, rubber molecular chains can be broken, their free volume can be increased, and the additives can be more evenly distributed and stabilized in the rubber matrix, avoiding adverse effects caused by aggregation. It can also improve the processing performance of rubber. High speed shearing exposes the molecular chain ends of rubber to generate new active groups, enhances their interaction with formula additives, and improves the processing performance of rubber, such as heating liquefaction performance. Thin pass can also change the viscoelasticity of rubber: high-speed repeated thinning damages the three-dimensional network structure of rubber, reducing its high elasticity and high viscosity; Appropriate thinning can enhance the flowability of rubber, achieve ideal viscoelastic balance, uniformity, and delicacy, thereby improving the physical and mechanical properties and service life of the rubber material. Rubber thin pipes play an important role in improving material properties, processing performance, and product quality
The process of mixing recycled tire rubber is of great significance for cost control, improving material performance, improving production process efficiency, and product quality. By optimizing the production and processing parameters of mixed rubber, the advantages of tire recycled rubber process can be maximized. The mixed rubber process plays an important role in improving the utilization rate of recycled rubber and reducing production costs
Exclusive original article [commercial authorization] reprint, excerpt and excerpt in any form are prohibited without written authorization. Focus on Hongyun rubber: learn the process formula and raw material technology of producing rubber products from recycled rubber to help you reduce costs and increase profits