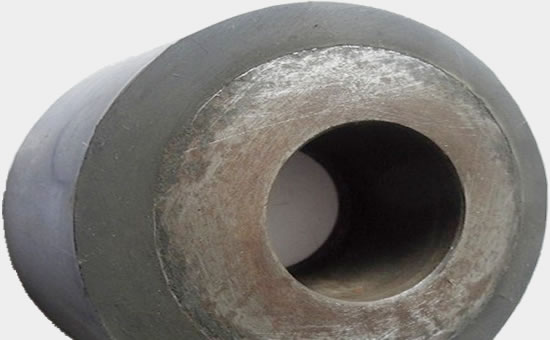
The rubber roller is made of metal or other materials as the roller core and rubber coated. It is an important component commonly used in industrial production, office equipment, household appliances and other fields. Industrial rubber rollers are mostly large rubber rollers. Vulcanization is an important process in the production process of rubber rollers, which directly affects the performance of the finished rubber rollers. There are big differences in rubber raw materials and sizes for large rubber rollers in different applications. Reclaimed rubber is used for production. For rubber rollers, the vulcanization method and vulcanization parameters need to be reasonably selected according to actual needs.
1. Rubber roller vulcanization heating method
Large rubber rollers are generally vulcanized in a vulcanizing tank. The heating method during vulcanization is mainly steam, in addition to hot air and hot water. Rubber rollers with special requirements due to the metal core contacting water vapor generally use indirect steam vulcanization, such as hollow iron core rubber rollers; for rubber rollers that cannot be vulcanized in a vulcanizing tank, hot water vulcanization is more preferred.
In order to prevent the rubber and metal core from delaminating the rubber roller and the roller core due to the difference in thermal conductivity, the rubber roller and the roller core are usually vulcanized slowly. In order to reduce the unevenness of the rubber layer performance, the rubber roller is vulcanized. It should be controlled at low temperature, that is, low temperature and long time vulcanization, it is recommended to use stepped vulcanization and temperature rise method.
2. Rubber roller vulcanization time setting
In actual production, due to the different sizes of rubber rollers, it is necessary to comprehensively consider the vulcanization time and other parameters according to the material and size of the roller core material, the vulcanization curve of the rubber formula, and the thickness of the rubber layer. Generally, the vulcanization time of the rubber roller is longer than that of the rubber. The vulcanization time required by itself is much longer. In order to achieve uniform vulcanization inside and outside and make the thermal conductivity of the metal core and rubber similar, the large rubber roller stays in the tank for up to 24-48 hours, which is 30-50 times the vulcanization time of ordinary rubber products.
3. Rubber roller vulcanization mechanical rotating device
During the vulcanization process of the large rubber roller, the rubber material is heated, which may cause the rubber material to sag, and in severe cases, it may fall off from the roller core. Therefore, it is recommended to use a mechanical rotating device to assist in the vulcanization of the large rubber roller to achieve uniform vulcanization. In order to improve the production efficiency of the rubber roller vulcanization process, many rubber roller factories will choose to close the heating and pressurizing equipment after vulcanization for an appropriate time, make full use of the residual temperature and pressure of the vulcanizing tank and the thermal hysteresis effect, make reasonable use of the evening time, and save The labor cost can prevent the hot glue roller from shelling after the rapid cooling after it is out of the furnace, so as to better guarantee the product quality.
When mixing reclaimed rubber to produce rubber rollers, you need to pay more attention to the above four aspects. Communicate with the 2YLYY730 reclaimed rubber manufacturer in advance about the characteristics of the reclaimed rubber, and do the performance index test of the reclaimed rubber in advance. It is best to find the reclaimed rubber manufacturer to provide the vulcanization formula ( (Vulcanization time, vulcanization temperature, vulcanization pressure, etc.) In this way, waste products can be reduced in actual production, production efficiency can be improved, and raw material costs can be reduced.
Exclusive original article [commercial authorization] reprint, excerpt and excerpt in any form are prohibited without written authorization. Focus on Hongyun rubber: learn the process formula and raw material technology of producing rubber products from recycled rubber to help you reduce costs and increase profits