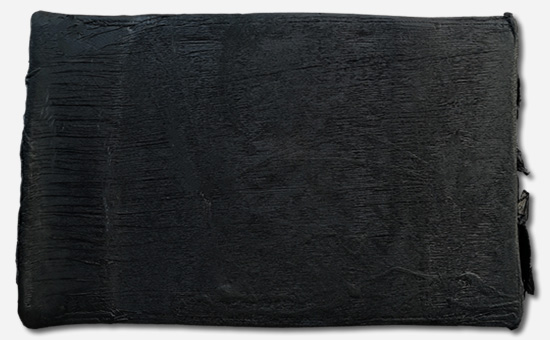
The recycled tire rubber is made from the rubber part of the waste tire and processed in three main sections: crushing, recycling and refining. It can be recycled into the production of rubber products, such as tire outer tire, rubber plate, rubber hose, triangle belt, conveyor belt, shoe material, rubber miscellaneous parts, etc., which can effectively reduce the production cost. When different rubber products are mixed with recycled tire rubber, the indicators and dosage of the selected recycled tire rubber are different. The rubber product manufacturer can test the indicators of the recycled tire rubber by test.
The test formula and test procedure are from GB/T 13460-2016 Recycled Rubber.
1. Test formula of tire recycled rubber
300g recycled tire rubber, 2.4g accelerator TBBS, 7.5g indirect zinc oxide, 1g stearic acid, 3.5g sulfur; Total: 314.4g.
2. Test procedure for tire regeneration rubber
(1) Molding
Adjust the roller temperature of the open rubber mixing machine in accordance with the provisions of GB/T 6038 to (40 ± 5) ℃, the roller pitch to (1.50 ± 0.10) mm, and the distance among the two baffles to (150 ± 20) mm (except for the roller pitch, the roller temperature of other rubber mixing procedures and the distance among the two baffles are set according to this setting). Take no less than 310g of qualified tire recycled rubber 2SLYY221 sample, put the sample into the rubber mixer and completely pass through the roller for three times, and place the plastic on a flat, clean and dry metal surface to cool to room temperature.
(2) Mixing
Weigh 300g of the recycled rubber sample of the plasticated tire and put it into the rubber mixer. Repeat the 3/4 cutter, fold the lower piece and then roll it, so that the sample is evenly distributed and wrapped on the roller.
When there is no obvious free powder on the surface of the accumulated rubber or the roller, make a full cut and fold the lower sheet, use the folded sample to scrub and absorb the mixture scattered on the rubber mixer chassis, and then put it into the rubber mixer vertically. After the mixture is mixed evenly, thin pass and take out the tablet. The mixed rubber should be prevented from cooling to room temperature on a flat, clean and dry metal surface. The cooled rubber should be wrapped with aluminum foil or other suitable materials to prevent contamination by other materials.
Recycled rubber mixing raw material sequence: accelerator [fold lower sheet once, rubber mixing duration 1.0min, roll pitch (1.5 ± 0.10) mm] → zinc oxide [fold lower sheet once, rubber mixing duration 2.0min, roll pitch (1.5 ± 0.10) mm] → stearic acid [fold lower sheet once, rubber mixing duration 1.0min, roll pitch (1.5 ± 0.10) mm] → sulfur [fold lower sheet twice, rubber mixing duration 1.5min, roll pitch (1.5 ± 0.10) mm] → thin pass [Number of times to fold the lower sheet 3 times, rubber mixing duration 1.5 min, roller pitch (0.80 ± 0.20) mm] → sheet out [folding the lower sheet 1 time, rubber mixing duration 1.0 min, roller pitch (1.50-2.00) mm], the mixing process folds the lower sheet 9 times, rubber mixing duration 8.0 min.
(3) Vulcanization
The vulcanized test pieces were vulcanized for 10min, 15min and 20min respectively at the temperature of 145 ℃± 1. After vulcanization, the tensile strength and elongation at break of the recycled rubber of the tire were measured, and the value of the best vulcanization time among the three vulcanization times was taken.
To reduce the production cost of rubber products by using recycled tire rubber, the manufacturer of rubber products must select the appropriate recycled tire rubber. Later, the editor will continue to share with you the basic vulcanization formula of rubber products produced by recycled tire rubber.
Exclusive original article [commercial authorization] reprint, excerpt and excerpt in any form are prohibited without written authorization. Focus on Hongyun rubber: learn the process formula and raw material technology of producing rubber products from recycled rubber to help you reduce costs and increase profits